OEE(Overall Equipment Effectiveness),即设备综合效率,OEE是一项独立的指标,用来表现实际的生产能力与理论产能的比率,已成为衡量企业生产效率的重要标准,也是TPM(Total Productive Maintenance)实施的重要手法之一
, 它旨在通过准确跟踪实现“完美生产”的进度来支持TPM计划
, 在日韩欧美的制造业和深度导入精益生产的中国企业已得到广泛应用。
大多数中小企业并不计算设备综合效率OEE,一方面是因不太懂设备综合效率OEE的计算方法,另一原因是计算设备综合效率OEE涉及数据信息较多难以计算,所以大多数企业管理者并不清楚设备的效率到底是多少。当员工说设备产能不够用时,老板就买台新的设备。据专家调研,中小企业中约70%以上企业的设备综合效率OEE处于35%~55%之间,只需要提升设备综合效率OEE便可以不需购买新设备便能有效解决工厂的产能不足问题。
云韬LDMES中TPM功能大大地简化了设备综合效率OEE的计算,只需在生产过程中用手机扫设备码记录下设备的使用数据即可以获取设备综合效率OEE数据,无需人工计算,使OEE数据的普及变得更轻松。
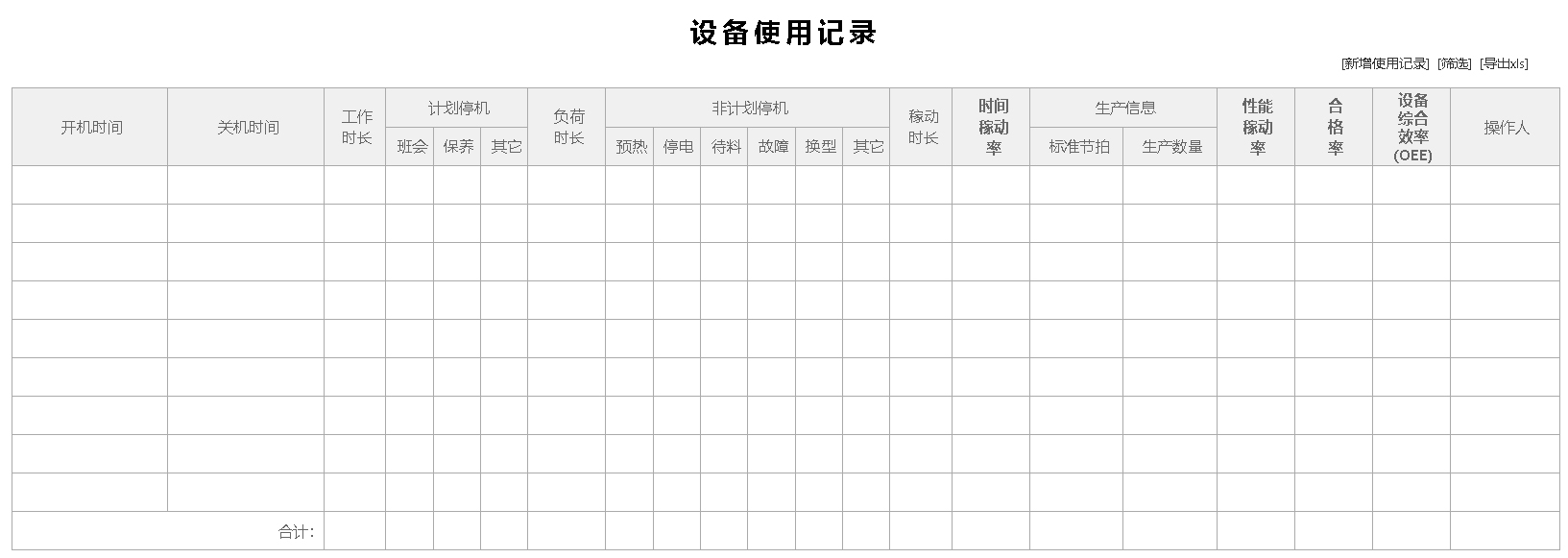
01、OEE计算
OEE = 时间稼动率 × 性能稼动率 × 合格品率
在OEE公式里,时间开动率反映了设备的时间利用情况;性能开动率反映了设备的性能发挥情况;而合格品率则反映了设备的有效工作情况。
反过来,时间开动率度量了设备的故障、调整等项停机损失,性能开动率度量了设备短暂停机、空转、速度降低等项性能损失;合格品率度量了设备加工废品损失。
计算举例:
某工厂实施8小时作业体制,其中中午休息1小时,上班时间包括早会,检查,清扫等20分钟,上、下午期间各休息15分钟。
有一台设备,因应市场需要,每天加班30分钟,该设备理论节拍为0.8分钟,在正常稼动时间内应生产575件,但实际仅生产出418件,实际测得的节拍为1.1分钟,当天更换刀具及故障停机时间为70分钟。
不良率维持2%。
请问该设备的设备综合效率为多少?
计算:
A: 实际作业时间 =480+30=510min
B: 计划停止时间 50min
C: 负荷时间 510-50=460min
D: 停机损失时间 70min
E: 稼动时间 C-D=390min
G:生产量418件
H:良品率 98%
I:理论节拍0.8
时间开动率 = (460-70)/460 = 84.8%
性能开动率 = (0.8*418)/390 = 85.7%合格品率 = 98%
于是得到 OEE = 84.8% ×85.7%×98% = 71.2%
02、OEE的实质
如果追究OEE的本质内涵,其实就是计算周期内用于加工的理论时间和负荷时间的百分比。
请注意,当展开OEE公式,有 OEE = 时间开动率×性能开动率×合格品率 =(开动时间/负荷时间) ×(加工数量×实际加工周期 /开动时间)×(理论加工周期/实际加工周期)×(合格产量/加工数量)= (开动时间×加工数量×实际加工周期×理论加工周期×合格产量)/(负荷时间×开动时间×实际加工周期×加工数量)约去分子、分母的公因子,OEE = (理论加工周期×合格产量)/负荷时间 = 合格产品的理论加工总时间/负荷时间,这也就是实际产量与负荷时间内理论产量的比值。
03、利用OEE进行损失分析
既然上述的计算方法可以如此简单,那么为什么要用这么复杂的公式呢?主要是为了分析问题。计算OEE值不是目的,而是为了分析六大损失。
设备的OEE 水平不高,是由多种原因造成的,而每一种原因对OEE的影响又可能是大小不同。在分别计算OEE的不同“率”的过程中,可以分别反映出不同类型的损失。
进一步,我们还可以结合运用PM分析方法,对 OEE不高的原因进行分析。
例如,当设备的 OEE水平不高,从 OEE计算看出是时间开动率低下,于是将时间开动率用方框框起来,再问为什么时间开动率不高,发现是设备故障引起,再继续往下分析,直到找出根本原因为止。
04、OEE计算中遇到的困难和解决方案
我们在计算OEE时,遇到计划停机以外的外部因素,如无订单、停水、电、气、汽等因素造成停机损失,常不知把这部分损失放到哪部分去计算。
有人把它们列入计划停机,但它们又不是真正意义上的计划停机。如果算做故障停机,但又不是设备本身故障引起的停机。
各个企业的计算五花八门,失去相互的可比性。当我们把OEE的计算作一扩展,给出“设备完全有效生产率(TEEP)”这一新概念和新算法,上述的问题可以迎刃而解。
05、在引入TEEP条件下OEE公式的修正
在引入TEEP条件下, 因为我们已经把非设备因素(即设备外部因素)引起的停机损失分离出来,作为利用率的损失来度量,故在计算OEE时,设备的时间开动率就要做相应调整。
在TEEP计算中
设备利用率=(日历工作时间 - 计划停机时间 - 设备外部因素停机时间) / 日历工作时间
正确的OEE计算,应该有设备时间开动率= 开动时间 / 负荷时间
其中,负荷时间=日历工作时间 - 计划停机时间 - 设备外部因素停机时间
开动时间=负荷时间 - 设备调整初始化时间(包括更换产品规格、更换工装模具、更换刀具等活动所用时间)
其他公式的算法和项目内容不变。
这样计算得到的 OEE可以准确反映设备本身的问题,能够客观评价企业的设备管理水平,同时也不会使企业之间的OEE因理解与算法不同而不可比。
如果要全面反映企业设备效率,即把所有与设备有关和无关的因素都考虑在内,则可以通过TEEP来反映。
06、企业OEE计算疑惑辨析
根据众多企业的统计和计算实际,提出将OEE公式的计算方法加以修正。
原来的:
★ 负荷时间 =日历工作时间 -计划停机时间
现在修正为:
★ 负荷时间 =日历工作时间 -计划停机时间 -非设备因素停机时间
原来的
★ 开动时间 =负荷时间 -故障停机时间 -安装、调整和初始化停机时间, 仍保持不变
上述的“非设备因素停机”包括开工不足停机、等待订单、等待计划排产、因企业系统管理不善或外部环境而造成的停水、停电、停汽、停气,使需要上述供给的设备停机。
上述的停机损失并不属于停机设备本身的问题,而是大系统对设备的影响。
上述的“计划停机”应界定为设备生产前后的例行保养,如加油、加冷却剂、停机点检、清扫、紧固、升温、预热、升速等活动。
计划停机应不包括因更换产品而造成的工、模、夹具更换,设备参数调整所造成的停机。
这样修正之后所计算得到的 OEE,基本反映了设备本身人-机系统的维护状况。而全面设备效率发挥状况可以由完全有效生产率来反映。
★ 完全有效生产率 =设备利用率×设备综合效率( OEE)
其中,设备利用率=(日历工作时-计划停机时间-非设备因素停机时间)/ 日历工作时间,由此看出,完全有效生产率把因为设备本身保养不善的损失和系统管理不善、设备产能不平衡、企业经营不善损失全面地反映出来。
而OEE的计算公式则主要反映了设备本身的系统维护、保养和作业效率状况。
上述OEE的计算中,合格品率既反映了设备状况不良损失,又反映了操作、工艺执行、参数控制方面的损失。
从设备管理的角度来看,合格品率不一定全面、真实地反映设备维护、保养水平。
建议引入一个纯设备合格品率的概念,即纯设备合格品率 =合格品数量/(生产数量-非设备因素废品数量)
由此引出了纯设备OEE的概念,简记为 OEE纯。
★ OEE纯 = 时间开动率 × 性能开动率 × 纯设备合格品率
这里的时间开动率是上述经过修正的公式,性能开动率的定义不变。OEE 纯更集中反映了设备维护、保养水平。完全有效生产率的公式不必修改。
OEE纯仅仅是为了集中、客观反映设备维护、保养水平。
因为完全有效生产率就是全面反映设备的总效率状况,没有必要分清哪些是因为设备,哪些是来自设备以外的因素。
另外有些企业在OEE计算时,出现了性能开动率大于 100%的状况,甚至有的高达 150%。
众所周知,性能开动率 =净开动率×速度开动率,其中,性能开动率=(生产数量×实际加工周期)/ 开动时间。
性能开动率反映了实际加工产品所用时间与开动时间的比例,它的高低反映了生产中的设备空转,无法统计的小停机损失。
净开动率是不大于100%的统计量。问题就出在速度开动率上。
★ 速度开动率 =理论加工周期 / 实际加工周期
原则上,理论加工周期不大于实际加工周期,即速度开动率是不大于100%的统计结果。
有的企业设备加工运转速度超出了设计速度,这样使速度开动率超过 100%,进而使性能开动率超过 100%。
我们认为,速度开动率超过 100%是不合理、也是不可取的。
理由如下:
1)如果设备开动速度超过了设计速度,就如同设计负荷5吨的大桥开过8吨的汽车一样,是掠夺性的使用设备,是不可取、不科学的做法,不应提倡。
2)若设备的原设计指标保守,根据实际,设备开动速度可以提升。
经过论证,这种提升不会造成对设备的损坏。那么,应该改变设备的设计速度指标,即理论加工周期,使速度开动率始终保持为一个不大于100%的统计结果。
3)因为异常提升设备运行速度(使设备过早进入耗损故障状态)造成速度开动率不正常的夸大,得到较高的OEE水平,掩盖了设备维护不当等问题,可能误导企业,不利于激发设备管理者对人—机系统六大损失的攻关和控制。
总之,让OEE应保持为一个不大于 100%的统计量,可以激发企业始终不渝地致力于 OEE的提升。